We’re experts and innovators focused on solving challenges, embracing change and growing.
Q&A with Peter Thommassen
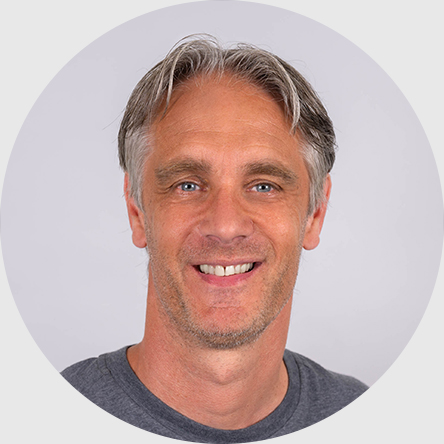
What inspired the creation of Pearls™ tinting technology?
In Europe, we observed that customers using traditional tinting machines faced persistent challenges such as mold, thickening, and drying, primarily due to lower colorant consumption. At the same time, increasingly stringent regulations for liquid colorants added complexity to the industry. To address these issues, our team brainstormed and developed the innovative Pearls solid tinting system. The goal was to create a solution that not only resolved these problems but was also user-friendly—similar to a coffee machine. Pearls dissolve quickly and are dosed volumetrically, offering a practical and efficient alternative to traditional liquid tinting systems.
Can you provide a simplified explanation of how Pearls are made in the production process?
The process begins similarly to producing a typical liquid colorant—we create a water-based pigment dispersion, known as the liquid feed. However, unlike conventional liquid colorants, the Pearls liquid feed uses fewer raw materials, excluding biocides, humectants and most additives. Next, this liquid feed is drip-cast into a tall tower cooled with liquid nitrogen. As the droplets fall, they freeze and are collected at the bottom on a sieve, where we separate the usable Pearls from particles that are too large or small. The frozen Pearls are then placed in a freeze dryer, where the ice (water) is removed through sublimation, leaving behind dry, porous Pearls. Finally, these Pearls are packaged in 2-liter recycled PET bottles, ready for use.
How is Pearls a sustainable alternative to traditional tinting systems?
Pearls’ overall environmental impact is significantly lower compared to traditional tinting systems. Although we are still finalizing our extensive lifecycle analysis, we know that from cradle to grave, Pearls solid colorants achieve a significant reduction in CO₂ emissions compared to liquid colorants. This is due to factors such as reduced waste, a longer shelf life, fewer raw materials in the formulation and a higher pigment load, making Pearls a more sustainable solution in the long run.
I believe we are only beginning to unlock the full potential of the dry tinting concept that Pearls represents.
Why did you choose volumetrically dosing over gravimetric dosing technology when developing Pearls?
There are several reasons we opted for volumetric dosing:
- Volumetric dosing allows for simultaneous dispensing of multiple colors, while gravimetric dosing can only handle one color at a time, as it requires a scale. This makes volumetric dosing much faster.
- An accurate scale for gravimetric dosing is expensive and slow, which would increase the cost of the tinting machine compared to current liquid dispensers. In contrast, our volumetric Pearls dispensers rely on gravity, eliminating the need for costly pumps or scales. This not only reduces the cost of the Pearls dispensers but also makes them more robust, requiring much less maintenance.
How did customer needs or market trends influence the development of Pearls technology?
Several market trends played a key role in shaping the development of Pearls technology. In Germany, a growing demand for biocide-free paints created the perfect opportunity for Pearls, as they are naturally biocide-free. Additionally, in Europe, stricter regulations aimed at reducing the use of biocides and limiting certain types of chemicals further accelerated the adoption of Pearls. Finally, the ease of use and low maintenance of the Pearls dispenser, compared to traditional dispensers, made it an even more attractive solution, driving the popularity of the Pearls concept.
What do you envision for the future of Pearls R&D efforts?
I see the next few years as a period of expanding our colorant offerings, building on the current technology. However, I believe we are only beginning to unlock the full potential of the dry tinting concept that Pearls represents. There are certainly many more applications beyond architectural waterborne coatings where Pearls can be used. Ultimately, our goal is to develop a universal Pearls technology that works across both water- and solvent-based coatings, making it suitable for a wide range of architectural and industrial applications.