We’re experts and innovators focused on solving challenges, embracing change and growing.
Discover the savings with Cool Colors
Construction industry leaders today are focused on showing how their services benefit customers, driven by the need to stay competitive, create jobs, innovate, and achieve cost efficiency and sustainability. From the materials used to the technologies implemented, every choice impacts a construction project’s performance, eco-friendliness, and, ultimately, the bottom line. That is why we created a complement to Vibrantz’s Cool Colors product line: the Cool Colors Savings Calculator.
Homes and businesses guzzle energy, particularly when it comes to keeping cool. In fact, air conditioning (AC) uses almost 20% of the electricity in buildings worldwide. This puts a strain on power systems and raises utilities costs for city residents. The urban heat island effect, caused by buildings and roads absorbing and holding heat, makes city temperatures higher than those in rural areas.
One strategy to mitigate the urban heat island effect and spare end-users from increased utility and maintenance costs is to use infrared reflective surfaces in exterior projects. Now, builders and paint producers can gain a competitive edge by showing their customers just how much how Vibrantz’s Cool Colors can reduce their energy bills and environmental impact.
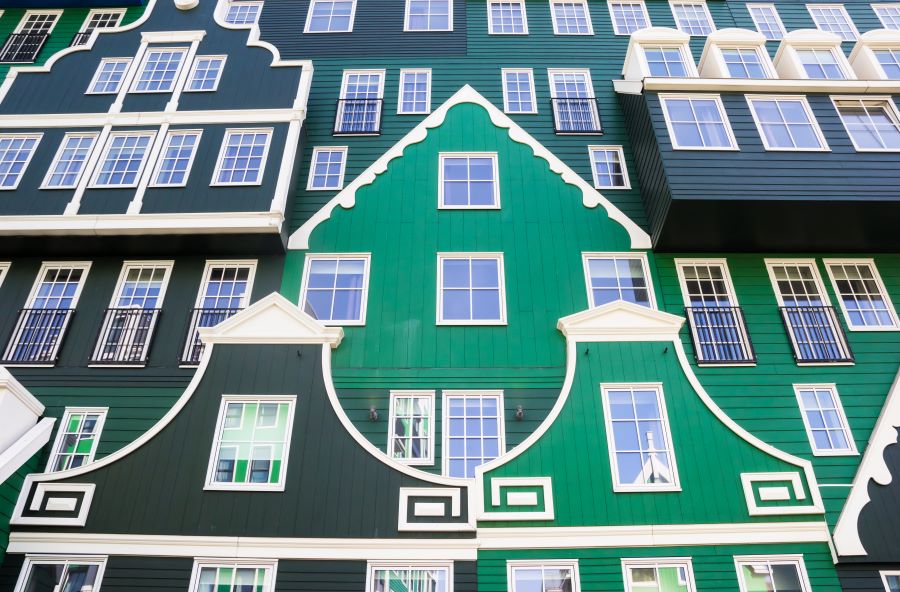
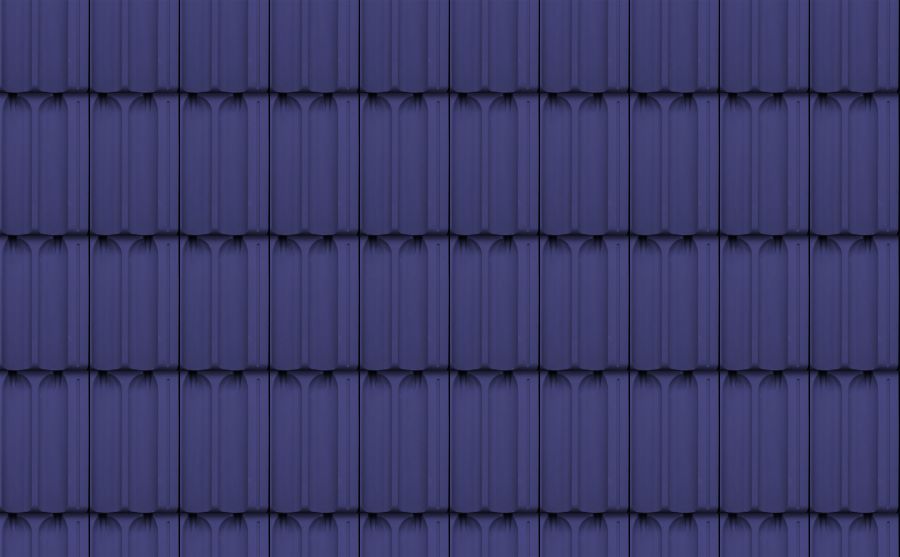
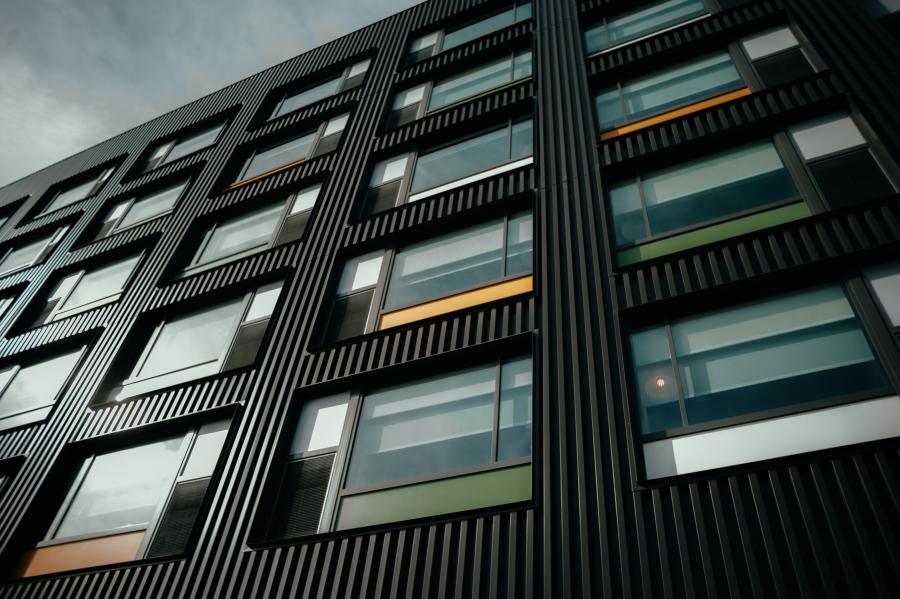
Cool Colors optimize savings
Vibrantz is a leading supplier of Cool Colors pigments for construction applications. Cool Colors do more than add aesthetic appeal; they are functional coatings that improve the energy efficiency of buildings by up to 20%. Compared to traditional coatings, Cool Colors reflect more sunlight and absorb less heat, resulting in lower energy bills, enhanced comfort for occupants, and a smaller carbon footprint.
Ideal for urban environments and hotter climates, Cool Colors applications include:
- Exterior paints for floor, roofs, walls and façades
- Asphalt coatings, asphalt roofing shingles and cement materials
- Outdoor plastic components, including furniture, fixtures, and other exterior elements
Cool Colors are proven to:
- Save energy
- Lower utility costs
- Improve comfort by reducing indoor temperatures
- Enhance the durability of exterior materials, extending their service life
Our Cool Colors range includes a variety of shades, and our color experts are available to collaborate with customers to develop and test custom Cool Colors formulas. Using infrared-reflective (IRR) pigments, even dark shades can stay cooler by reflecting infrared radiation from sunlight—despite appearing just as dark to the naked eye.
Cool Colors have long been a cornerstone of energy-efficient construction, and our innovative new calculator tool enables customers to understand the tangible benefits for building and construction projects. Seeing is believing, and our new calculator makes it clear how Cool Colors can cut down on energy use, lower electricity bills and contribute to a more sustainable future.
Introducing the new Cool Colors Savings Calculator
To help quantify the benefits of Cool Colors, we developed a user-friendly Savings Calculator in partnership with DEKRA Spain. This powerful tool allows customers to estimate the potential savings end users can achieve by incorporating Cool Colors into their construction projects.
Use our Savings Calculator is a tool to engage customers
- Data-driven decisions: Help them make informed choices backed by simulated data. The calculator provides estimates based on specific project parameters
- Cost efficiency: Show them the financial benefit of using Cool Colors, helping justify the investment
- Sustainability: Highlight the environmental benefits of Cool Colors, aligning projects with green building standards and sustainability goals
Explore the difference Cool Colors can make
Even small savings can add up to significant financial benefits for end users over time. Try our calculator tool to unlock the potential for greater efficiency and reduced costs. Contact us to customize a Cool Colors solution for your next build and or renovation.